What is Safety Stock?
First up, let's examine the core concept, definition, and purpose of Safety Stock.
Definition
In inventory management, safety stock acts as a buffer against uncertainty in demand, lead time, and supply. It's the minimum amount of inventory a business keeps on hand to mitigate the risk of stockouts.
Purpose
The main purpose of safety stock is ensuring continuous business operations and satisfying customer demand, even when unpredictable events disrupt regular supply or cause sudden demand spikes.
Importance
Safety stock represents a strategic decision by a company to absorb the variability in its supply chain. It guarantees customer satisfaction and ensures smooth supply chain operations.
Components
The main components involved in safety stock calculations are demand variation, lead time variation, and desired service level.
Types
Safety stock can be categorized based on its use into cycle stock (service regular demand), safety stock (buffers against variability), seasonal stock (handles predictable demand changes), and strategic stock (supports business strategies).
Who Needs Safety Stock?
Now, we'll explore which businesses or operations specifically would benefit from the use of safety stock.
Manufacturers
Safety stock is often vital for manufacturers to handle variability in their production process or supplier reliability, ensuring smooth operations.
Retailers
Retailers utilize safety stock as a buffer to satisfy customer demand when their inventory turnover is faster than the resupply speed.
Wholesalers
Wholesalers, who act as links between manufacturers and retailers, also need safety stock to deal with possible disruptions in their supply channels or changes in buying patterns.
E-commerce Platforms
Online businesses make extensive use of safety stock, as they deal with large amounts of inventory and experience variability in demand.
Supply Chain Managers
Professionals responsible for inventory management often use safety stock as a tool in their strategy against supply chain uncertainties and to maintain service levels.
When is Safety Stock Used?
Safety stock comes into play whenever there's uncertainty or variability in a supply chain. Let's explore these situations.
Demand Fluctuations
In case of unforeseen surges in demand, safety stock can prevent inventory shortages and missed sales opportunities.
Supply Disruptions
Supply chain disruptions, whether caused by supplier issues or unexpected events like natural disasters, can be mitigated using safety stock.
Seasonality
During peak seasons or sale events where demand usually outstrips regular supply, safety stock ensures customer satisfaction.
Transit Time Variations
Just-in-time deliveries fail when there are delays in transportation. Safety stock serves as insurance against these delays.
Manufacturing Delays
In case of manufacturing delays due to equipment malfunction or worker shortage, safety stock can keep the production operational.
Where is Safety Stock Applied?
It is essential to grasp the scope of safety stock application within various business sectors.
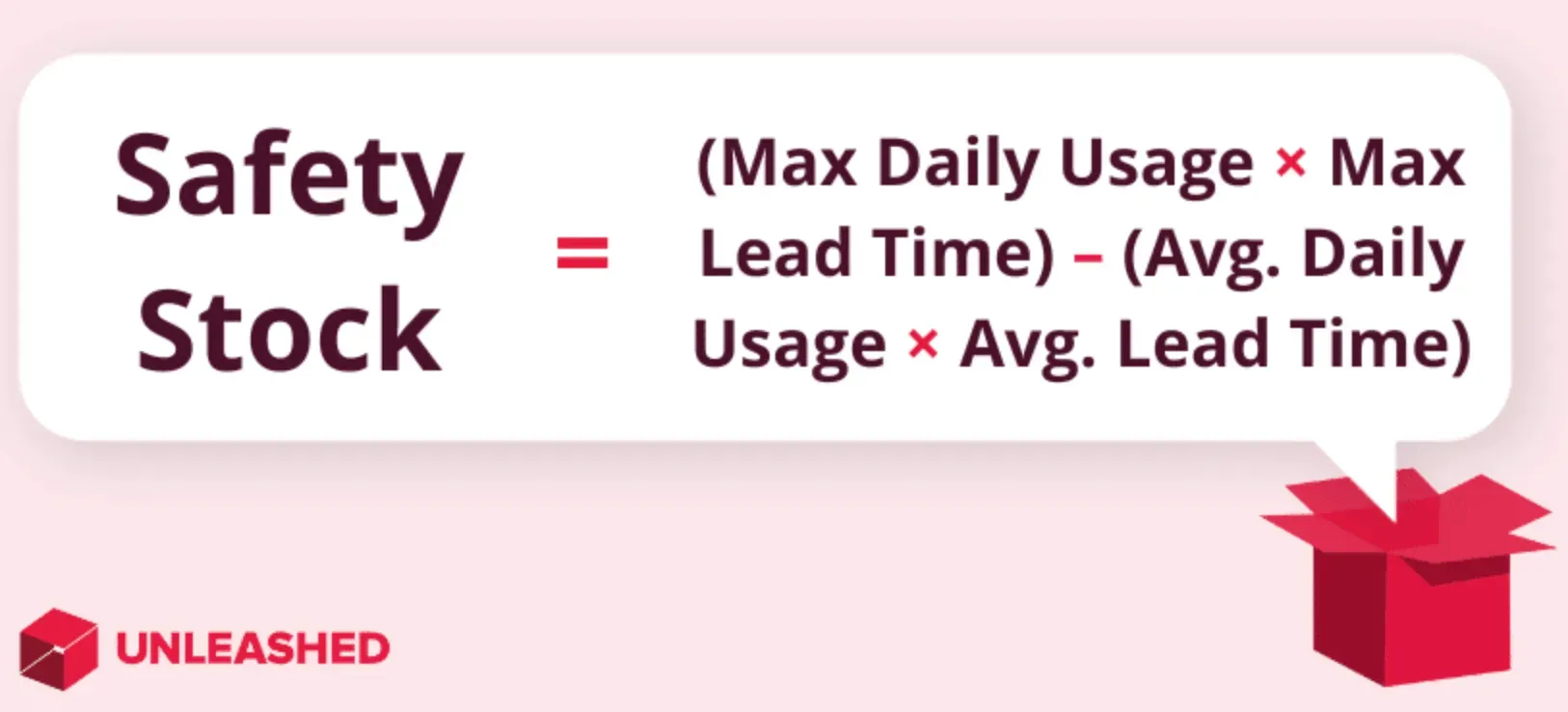
Retail
In the retail industry, safety stock is critical to provide a smooth shopping experience, avoid stockouts, and thus sustain profitability.
Manufacturing
For manufacturers, safety stock is essential for continued operations, avoiding assembly line disruptions due to a lack of raw materials or components.
Food Industry
In the food and beverage industry, safety stock is necessary to meet sudden demand spurts and handle perishable items with limited shelf life.
Automotive Industry
In the auto industry, an interruption in supply can halt the entire production line, making safety stock crucial.
E-commerce
For e-commerce operations, dealing with fluctuating demand and guaranteeing quick deliveries often requires maintaining safe stock.
How is Safety Stock Calculated?
Here are the common steps in calculating safety stock to secure your supply against variabilities.
Understand Demand and Lead Time Variability
The initial step involves understanding the demand and lead time variations. These are essential in predicting possible scenarios affecting your stock levels.
Decide on a Service Level
The service level represents the desired probability of not having a stockout. It affects the size of your safety stock — higher service levels result in larger safety stocks.
Calculation Using Formula
Safety stock can be calculated using standard formulas, considering factors like demand and lead time variability, service level, lead time, and demand period.
Continuous Review
Once the initial safety stock level is determined, it needs a continuous review based on evolving demand & supply conditions and the organization's strategy.
Perform Profitability Analysis
Understanding the cost implications of maintaining safety stock involves making a balance between the costs of holding safety stock and potential loss from not meeting demand.
Best Practices in Safety Stock Management
Let's dig into the best ways to manage safety stock effectively, ensuring you're prepared without tying up too much capital.
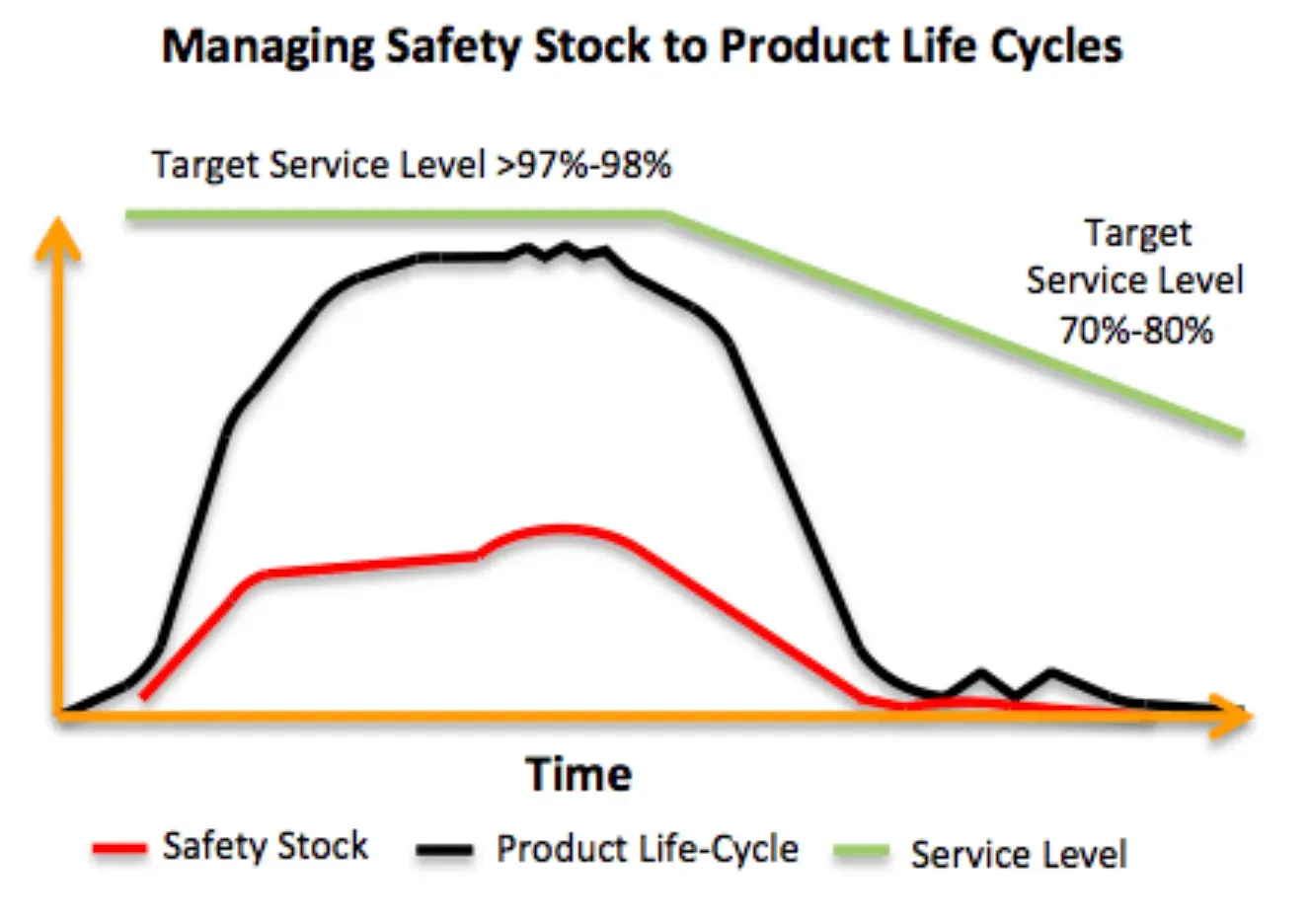
Regular Demand Forecasting
Updating and recalibrating your demand forecasting models shouldn't be a once-in-a-blue-moon affair. The trick is to use historical sales data, market trends, and predictive analytics.
For instance, anticipating seasonal spikes for a winter clothing line, based on sales patterns, can help you adjust safety stock levels before the chill sets in.
Supplier Relationship Management
Keeping in sync with your suppliers is like being in a solid relationship; it's all about communication. By working closely with suppliers to understand their lead times and capacity constraints, you could reduce the need for large safety stocks.
If your fabric supplier can promise faster restock times, you can keep less backup inventory of textiles.
Inventory Classification
Not all products are created equal in the inventory world. Employing methods like ABC analysis – categorizing items from most to least critical based on value and turnover rate – helps prioritize which items require more safety stock.
High-value items with slow turnover might need a thicker safety cushion than cheaper, fast-moving ones.
Effective Lead Time Management
The less time it takes for goods to get to you, the less backup stock you theoretically need. Simplify lead times by choosing local suppliers when possible or by streamlining internal receiving procedures.
For example, a furniture store might reduce lead times by pre-assembling items whenever they're low on orders, streamline the unloading process, or select local timber suppliers over distant ones.
Utilizing Inventory Management Software
Good software is like a trusty sidekick for managing safety stock.
It provides precise diagnostics of inventory levels, turnover rates, and sales forecasts with a few clicks, all based on real-time data. Imagine a bookstore that uses software to track popular titles; this software could potentially forecast sales dips and spikes, prompting efficient safety stock adjustments.
Challenges in Safety Stock Management
On the flip side, managing safety stock isn't a walk in the park. You might face some hurdles along the way.
Balancing Costs
Juggling the expense of holding safety stock (warehousing, insurance, potential obsolescence) against the risk of stockouts requires an acrobatic act.
This balancing can be quite nuanced, as overstocking increases costs, while understocking leads to lost sales and potentially lost customers.
Accurate Demand Forecasting
Predicting future demand with pinpoint accuracy is like trying to hit a moving target blindfolded, especially in volatile markets.
If a phone manufacturer overestimates the demand for a new model, they wind up with a warehouse of unused safety stock, taking up space and tying up capital.
Dealing with Variability
When it comes to lead times and demand, unpredictability is your constant, unwanted companion.
If you import electronics, and the new product gets delayed at the border, or a sudden tariff affects import speed, this variability throws a wrench into your safety stock calculations and overall inventory management.
Supplier Dependability
If your suppliers are as unpredictable as a game of chance, you're in for a rocky ride. Dependency on a single supplier is risky, as any disruptions on their end could immediately affect your inventory levels.
For instance, a restaurant that relies solely on a local organic farm for produce could face troubles if an unexpected frost nips the harvest in the bud.
Obsolescence Risk
In today’s fast-paced market, products can go from hot to not faster than you can say “clearance sale”. Tech gadgets, fashion items, or perishable goods, in particular, are susceptible to becoming obsolete.
An electronics retailer, for instance, might struggle to offload last season’s model if a new version is suddenly released.
Examples in Safety Stock Management
To put theory into real-world context, here are some examples across different industries.
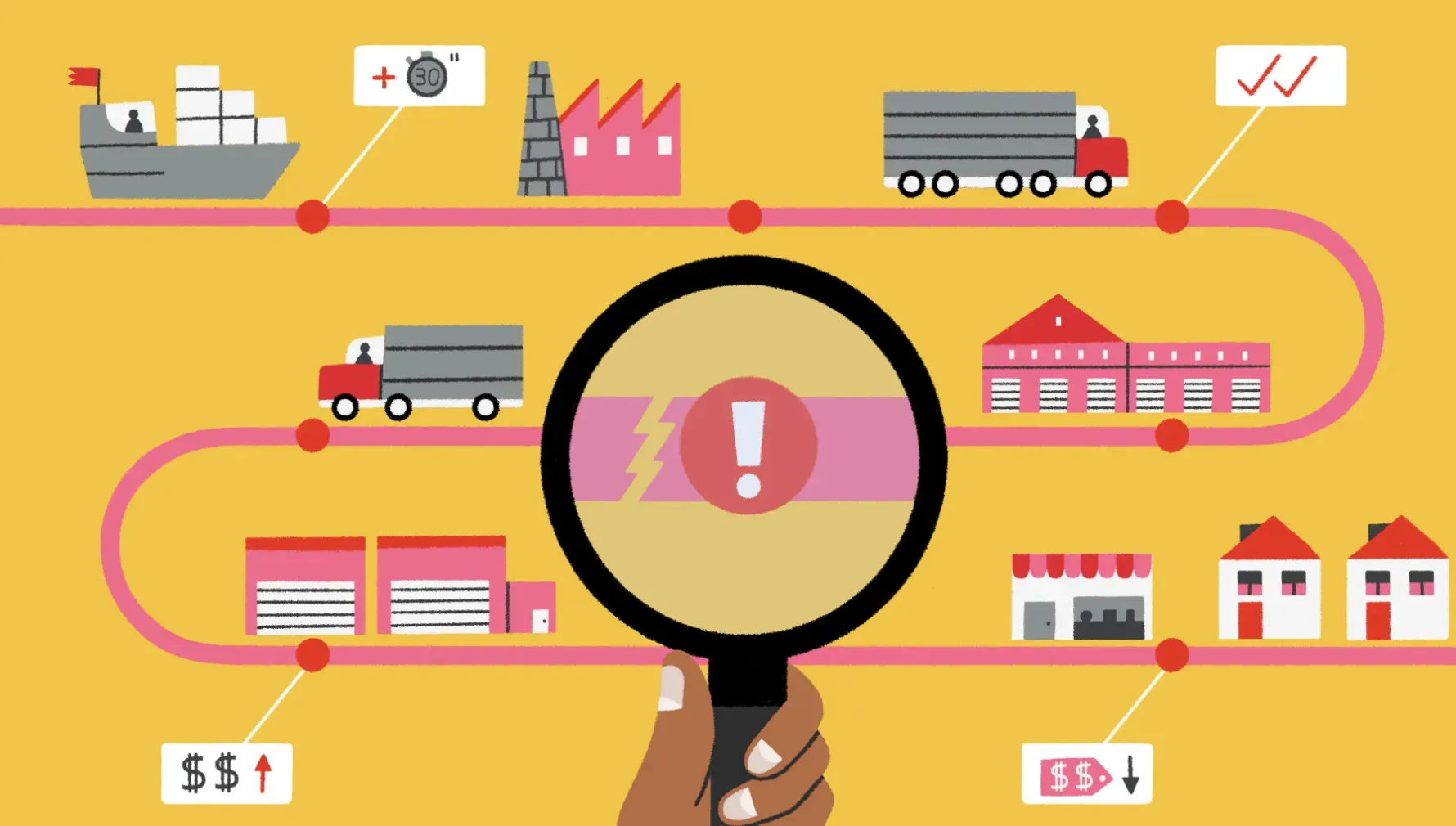
Retail
Imagine you manage a bookstore. A best-seller could unexpectedly go viral because a celebrity tweets about it. By implementing safety stock best practices, the store always has extra copies around, so they'll never miss out on a sale while keeping restocking costs optimized.
Manufacturing
A company manufacturing car parts may rely on specific electronic components that have a six-month lead time. By establishing robust safety stock, they can avoid shutdowns in the production line, which could cost a fortune and delay deliveries to automakers.
Food Industry
In the world of eateries, a popular seafood restaurant might need extra stock before a holiday weekend. However, the shelf life and the risk of spoilage require delicate balancing to avoid waste.
Automotive Industry
For auto manufacturers, safety stock is critical due to the high cost of an idle production line. Keeping safety stock for components like semiconductor chips could save the day when suppliers face shortages, as seen in recent global disruptions.
E-commerce
An online retailer specializing in seasonal goods, such as Christmas decorations, needs to master the use of safety stock. Too little and they miss out on peak sales; too much and they’re saddled with unsold stock until the next festive season.
Emerging Trends in Safety Stock Management
The field of safety stock management isn't static — new and emerging trends are constantly shaping it.
Advanced Analytics
The usage of predictive analytics and machine learning can improve demand forecasting, thus enabling businesses to optimize their safety stock levels.
Just in Time (JIT) Inventory Management
JIT inventory management aims to increase efficiency by receiving goods only when they are needed, thus reducing safety stock requirements.
Real-Time Inventory Tracking
Advancements in technology have enabled real-time inventory tracking, allowing for more precise safety stock calculations.
Supplier Collaboration
Increased collaboration with suppliers allows for better lead time and delivery accuracy, resulting in optimized safety stock.
Inventory Optimization Software
Emerging sophisticated inventory optimization software is enabling businesses to better control their safety stock levels, reducing both excess inventory and stockouts.
Frequently Asked Questions (FAQs)
Why Is Safety Stock Critical in Inventory Management?
Safety stock acts as a buffer against the unexpected—a safeguard from stockouts due to demand spikes or supply delays, ensuring smooth operations and customer satisfaction.
How Does Seasonality Influence Safety Stock Levels?
Seasonal trends drastically affect sales, so safety stock must be increased in anticipation of high-demand periods to avoid shortages and lost sales.
Can Just-In-Time (JIT) Practices Coexist With Safety Stock Strategies?
Yes, but cautiously. While JIT minimizes inventory, some safety stock might be needed to cover lead time variability and avoid disruptions in a lean supply chain.
What Role Does Lead Time Play in Calculating Safety Stock?
Longer lead times often require more safety stock as the time buffer needed to respond to variability in demand and supply is greater.
How Often Should Safety Stock Levels Be Reviewed?
Regularly review safety stock levels—at least quarterly—to account for changes in demand patterns, supplier reliability, and lead time consistency. Adjustments ensure optimal inventory health.