What is Inventory Management?
Inventory management is crucial to businesses that rely on raw materials, components, and finished products to create their offerings.
Essentially, it's the process of ordering, storing, processing, using, and selling a company's inventory.
Whether you’re in retail, eCommerce, manufacturing, or food services industries, inventory management will help you guarantee customer satisfaction while reducing inventory costs and wastage.
What is the Purpose of Inventory Management?
Having effective inventory management is essential when it comes to ensuring your business has a steady flow of inventory on hand without carrying too much or too little stock.
This reduces the risk of stockouts and inaccurate records. At the same time, you need to keep in mind that ordering too little or too much might cost you customers and money.
Benefits of Inventory Management
There are several benefits to having efficient inventory management:
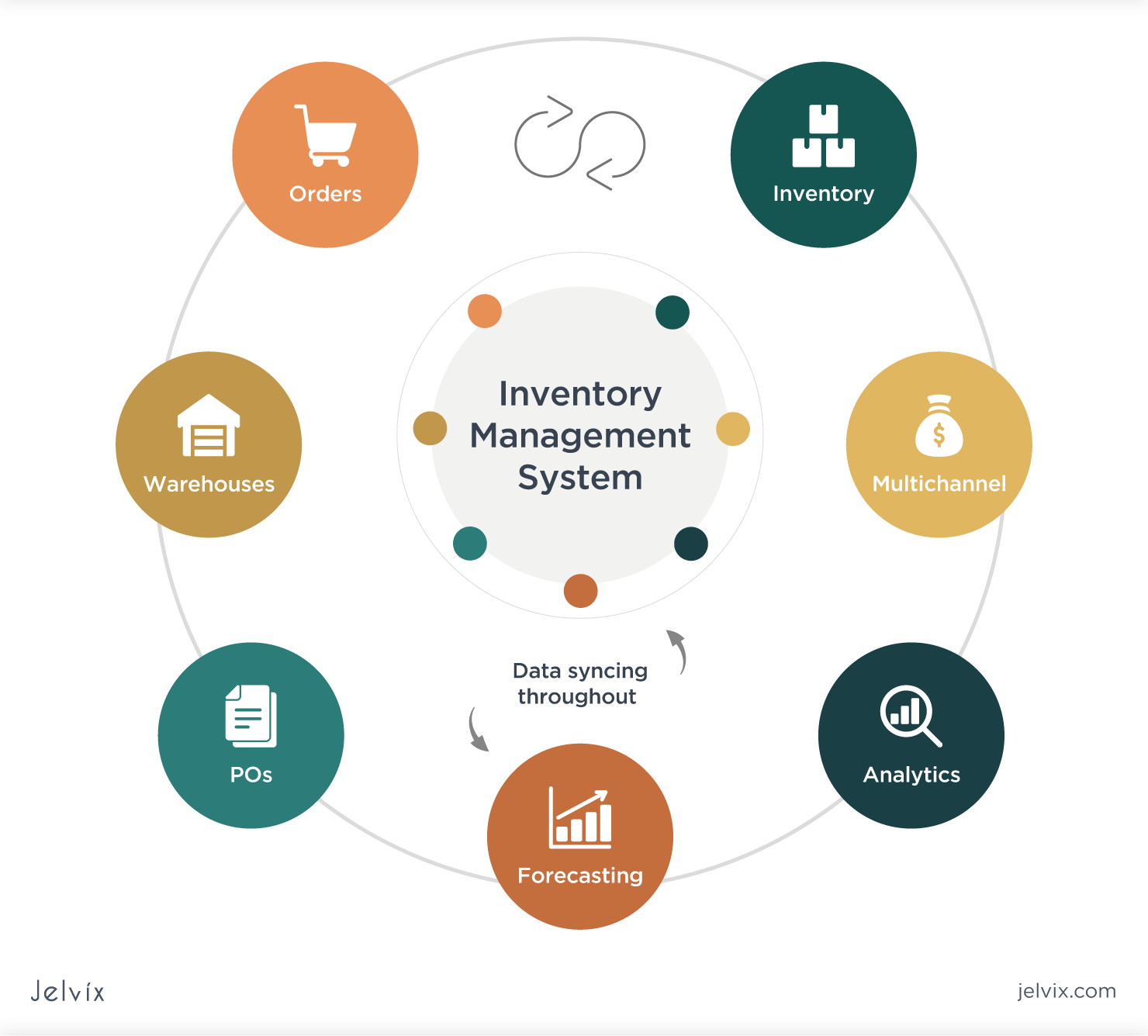
- Reducing costs of purchasing inventory and storing it.
- Saving on the opportunity cost that you’d incur if all your stock was sold out when a customer came with a big order.
- Increasing the sales of items that sell faster, thus improving your cash flow.
- Helping identify slow-moving products to avoid them becoming dead stock.
- Ensuring that customers can get the products they want promptly without having to wait for them to come back in stock.
The Process of Inventory Management
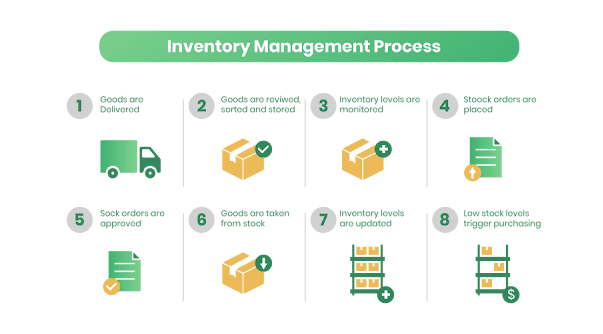
In order to effectively manage your inventory, you need to have a solid understanding of the inventory management process and its components.
Ordering of Inventory
Ordering inventory is the first step in the inventory management process. In this stage, you determine the quantity of each item you need to have in stock.
This can be done by analyzing historical sales data, predicting future demand, and considering any upcoming promotions or events.
Once you have determined the quantities needed, you place orders with your suppliers or manufacturers.
Storing of Inventory
Once the inventory has been delivered, it needs to be properly stored. This involves organizing the inventory in a way that makes it easy to locate and access when needed.
It may include using shelves, bins, or other storage systems to keep the inventory organized.
Additionally, proper storage conditions should be maintained to ensure the inventory remains in good condition. This may include factors such as temperature control, moisture control, and protection from damage.
Processing of Inventory
Processing inventory refers to the activities involved in receiving and verifying the incoming inventory.
This typically involves checking the received quantities against the purchase orders or packing slips, inspecting the quality of the items, and updating the inventory records to reflect the new stock.
It is important to accurately and efficiently process inventory to avoid discrepancies and ensure the availability of accurate data for decision-making.
Using of Inventory
Using inventory refers to the act of utilizing the inventory in your business operations. This can include bringing items out of storage, distributing them to the appropriate departments or locations, and incorporating them into production or service processes.
Proper usage of inventory involves tracking the movement of items and updating the inventory records accordingly. This helps in maintaining accurate stock levels and avoiding stockout or overstocking.
Selling of Inventory
The final step in the inventory management process is selling the inventory to customers. This can be done through various channels, such as a physical store, online platforms, or wholesale distribution.
Effective selling of inventory involves managing customer orders, processing sales transactions, and updating the inventory records to reflect the items sold.
It is important to regularly monitor sales performance and adjust inventory levels to meet customer demands and maximize profitability.
Types of Inventory Managed
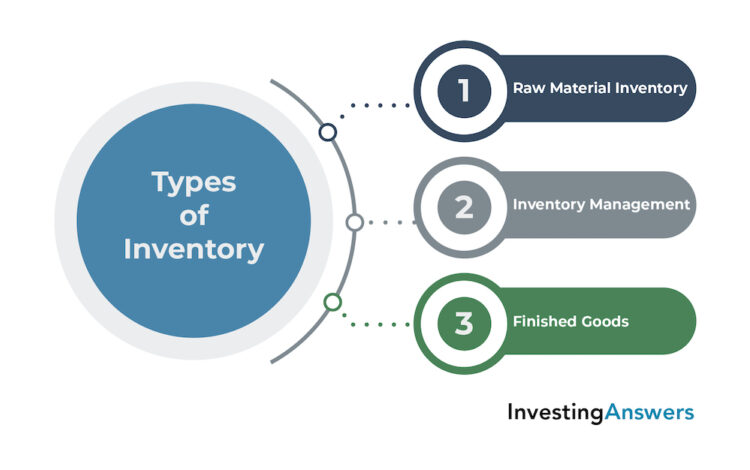
Different businesses have distinct types of inventory that they manage during the production process. The three primary types of inventory include raw materials, components, and finished products.
- Raw Materials: Raw materials are the building blocks that companies use to create their finished products. They are usually unprocessed materials that are required for the various production processes within a company.
- Components: Components refer to those parts that are made up of raw materials and are required for the larger manufacturing process. They are not ready for use and would have to be assembled.
- Finished Products: Finished products are the goods that are made by a company from raw materials and are ready for sale.
Risks Associated with Inventory Management
No matter how much you try to keep things under control, unforeseen circumstances may arise that could affect inventory management adversely.
- Stock Spoilage: Inventory that isn't sold before the expiration date carries significant risk. This is especially true for the food services industry or those dealing with perishable products.
- Theft: Inventory theft can be a significant problem for any business. Adequate security measures should be put in place to ensure the protection of inventory.
- Damage: Sometimes, inventory items may be damaged when they are not stored or handled appropriately. Such damages may lead to additional costs.
- Changing Customer Preferences: Customer preferences can affect a company's business operations, especially the inventory management process.
Strategies for Effective Inventory Management

Here are some strategies for efficient inventory management:
- Just-in-Time Inventory Management Strategy: This inventory management strategy involves keeping raw materials to a bare minimum to reduce overhead costs further.
It implies creating an adequate supply chain to ensure the availability of raw materials on demand.
- Pull Inventory Management Strategy: The customers are the driving force behind this inventory management strategy as businesses manufacture their inventory in response to a clear, existing demand. This strategy is helpful for companies that want to keep their inventory costs low.
- Push Inventory Management Strategy: In this strategy, brands manufacture products in bulk based on a forecasted expectation of consumer demand. The problem with this strategy is that if consumer demand is not as forecasted, it would not be easy to sell off the excess inventory.
Automation in Inventory Management
Automation has become increasingly prevalent in inventory management, with the integration of artificial intelligence (AI) playing a crucial role in optimizing operations.
AI allows businesses to streamline and automate various inventory management processes, improving efficiency and accuracy.
Artificial Intelligence in Inventory Management
AI can evaluate orders automatically and predict the best set of stocks needed to fulfil it. This approach increases the accuracy of inventory forecasting, making the inventory management process more efficient.
Automation in inventory management can improve the accuracy of forecasting sales trends, enhance demand forecasting, efficient replenishment, real-time inventory tracking and order fulfillment.
Enhanced Demand Forecasting
AI-powered systems can analyze historical data, market trends, and customer behavior to generate accurate demand forecasts.
By accurately predicting demand, businesses can optimize inventory levels, reducing the risk of stockouts or excess inventory.
Efficient Replenishment
Automation allows businesses to automate the ordering process based on predefined inventory thresholds.
AI algorithms can determine when and how much inventory needs to be reordered, eliminating manual calculations and potential human errors.
Real-time Inventory Tracking
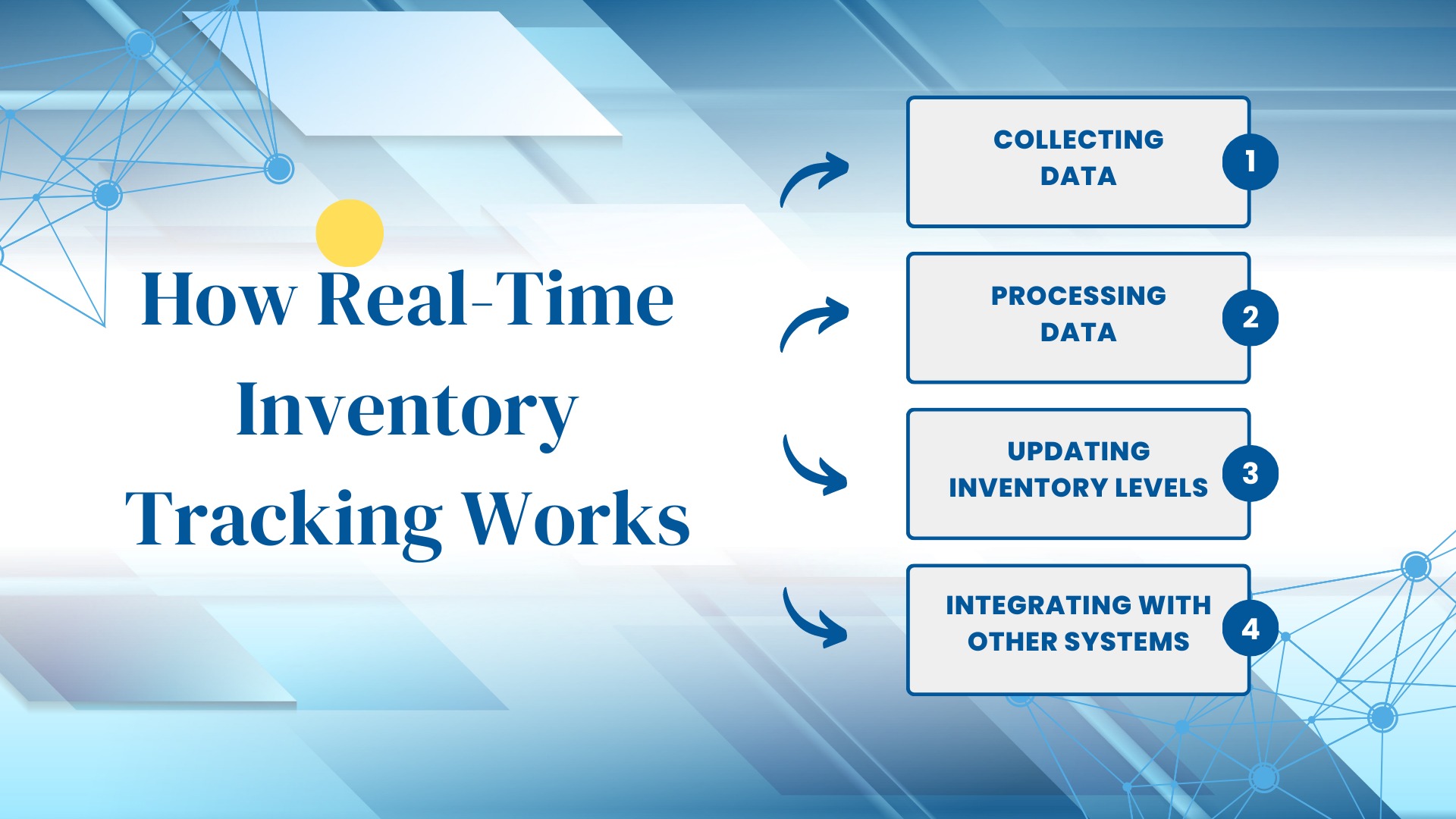
AI technology enables real-time tracking of inventory levels across multiple locations or channels.
This visibility allows businesses to monitor stock levels accurately, identify discrepancies, and adjust their replenishment strategies accordingly.
Improved Order Fulfillment
Automation systems can prioritize and optimize order fulfillment based on factors such as stock availability, customer location, and shipping costs.
AI algorithms can determine the most efficient way to fulfill orders, reducing lead times and improving customer satisfaction.
Common Inventory Management Problems and Solutions
Effective inventory management is crucial for businesses. Learn how to tackle stockouts, excess inventory, and deadstock to improve efficiency.
- Stockouts: To avoid stockouts, accurately forecast demand and maintain optimal inventory levels. Use inventory management systems, demand forecasting techniques, and monitor inventory levels closely.
- Excess Inventory: To tackle excess inventory, utilize inventory optimization techniques such as JIT inventory management, sales, and promotions.
Also, practice effective demand planning and regular inventory audits.
- Deadstock: Regularly review inventory to identify slow-moving or obsolete items. Implement markdowns or discounts to clear out deadstock.
Improve inventory forecasting accuracy and find alternative uses or channels for selling or disposing of headstock.
Frequently Asked Questions (FAQs)
How can I optimize my inventory levels?
To optimize inventory, regularly analyze sales data, set reorder points, and implement just-in-time strategies.
This allows you to balance stock availability with minimizing carrying costs.
What is safety stock, and why is it important?
Safety stock acts as a buffer against unexpected fluctuations in demand or supply chain disruptions.
It ensures you have enough inventory to meet customer demands and prevent stockouts.
What are the benefits of using barcodes in inventory management?
Barcodes streamline inventory tracking and reduce errors. They enable quick and accurate product identification, facilitate stock counting, and accelerate the receiving and shipping processes.
How can I manage multiple sales channels effectively?
To manage multiple sales channels, use an inventory management system that integrates with your e-commerce platforms.
This allows for centralized inventory control, order syncing, and real-time inventory updates across channels.
What is the role of forecasting in inventory management?
Forecasting helps anticipate future demand, allowing you to adjust inventory levels accordingly.
Accurate forecasting helps prevent overstocking or understocking and ensures efficient inventory replenishment.