Introduction to Reverse Logistics
Begin your reading with a basic introduction to reverse logistics.
What is Reverse Logistics?
Reverse logistics is like the recycling system for products. When you buy something and need to return it, reverse logistics kicks in. It's the journey products take in reverse, from the customer back to the seller or manufacturer.
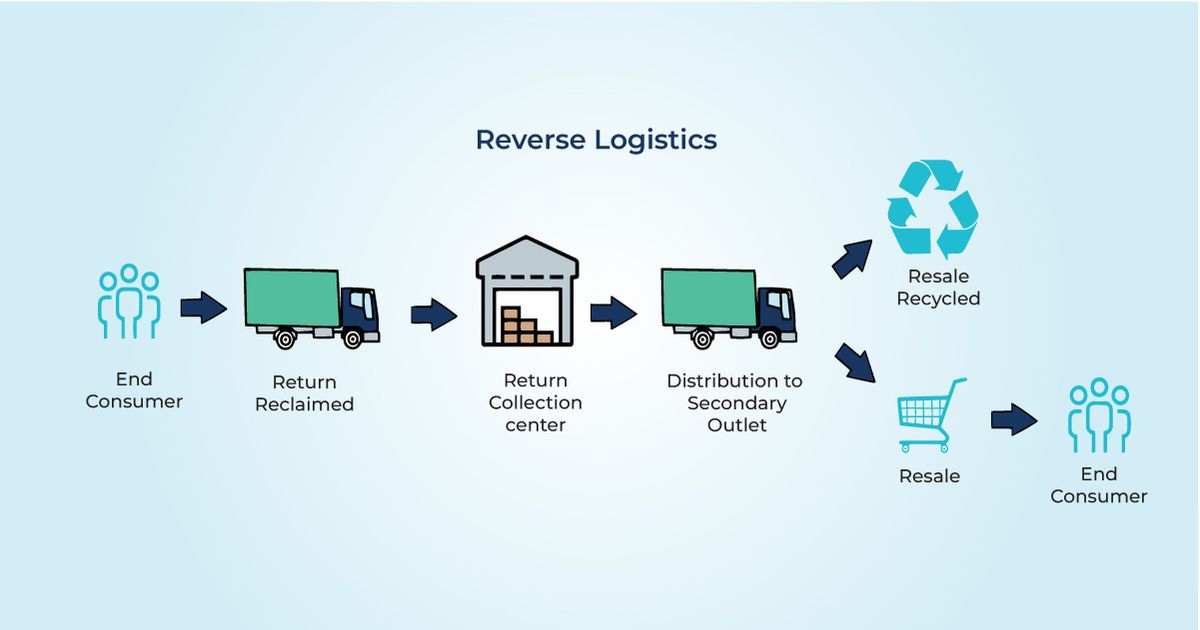
Importance of Reverse Logistics
Reverse logistics matters because it's not just about returns. It's also about what happens next: fixing, recycling, or safely disposing of products. This process can save money and help the planet.

The Process of Reverse Logistics
The process of reverse logistics services is as follows:
- Product Return Initiation: Customers request returns via online platforms or customer service.
- Return Authorization: Sellers approve returns based on their policies.
- Transportation Management: Arrangements for shipping the return items back to the seller or a designated facility.
- Receiving and Inspection: Returned items are received at the warehouse where their condition is assessed.
- Processing and Disposition: Deciding whether to restock, refurbish, recycle, or dispose of the returned item.
- Reverse Logistics Data Management: Collecting and analyzing data from returns to improve products and processes.
- Customer Refund or Replacement: Completing the process by either refunding the customer or sending a replacement product.
Types of Reverse Logistics
The types of reverse logistics services are as follows:
Returns Management
Returns are just the beginning. Managing them means figuring out the best way to handle returned items—whether they can be resold, repaired, or recycled.
Remanufacturing and Refurbishment
Some items need a little TLC before they're ready to go back out into the world. Remanufacturing and refurbishment are all about giving products a second chance.
Recycling and Disposal
Not everything can be fixed. That's where recycling and disposal come in. They're all about making sure products are dealt with in a way that's good for the planet.
Suggested Reading: Logistics Management
Benefits of Implementing Reverse Logistics
The benefits of implementing reverse logistics services are the following:
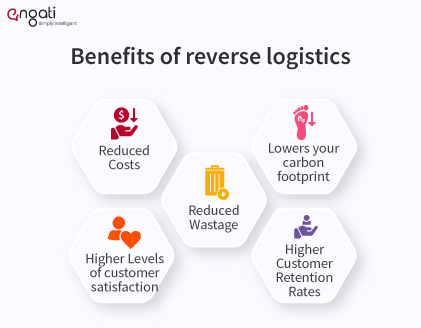
Cost Reduction
Implementing reverse logistics can lead to significant cost savings.
When you refurbish and reuse products, you're spending less on buying new ones. This can cut down on your overall expenses.
Sustainability and Corporate Responsibility
Being mindful of what happens to products after they're used shows that your company cares about the environment. Recycling and responsible disposal reduce waste and support sustainability efforts.
Enhancing Customer Relationships
Handling returns and repairs promptly and efficiently can make customers happy. It shows you value their experience and are committed to making things right. This can build trust and loyalty over time.
Strategies for Effective Implementation of Reverse Logistics
The strategies for effective implementation of reverse logistics are the following:
- Clear Return Policy Communication: Ensure customers understand the return process, criteria, and time frame clearly.
- Invest in Reverse Logistics Software: Utilize technology for managing returns efficiently, tracking products, and analyzing data for insights.
- Integrate Quality Control: Implement strict quality checks to reduce the volume of returns due to defects or inaccuracies.
- Optimize Transportation Routes: Use logistics strategies to minimize costs and carbon footprint in the transportation of returns.
- Foster Strong Vendor Relationships: Collaborate with vendors and suppliers for seamless processing and disposition of returns.
- Employee Training: Equip staff with the necessary skills and knowledge to handle reverse logistics processes effectively.
- Sustainability Practices: Focus on recycling, refurbishing, and waste reduction to improve environmental impacts and reduce costs.
- Monitor and Analyze Returns: Regularly review return reasons and rates to identify patterns and areas for product or process improvement.
- Customer Feedback Loop: Use insights from returns to enhance products and customer service, potentially reducing future returns.
- Flexible Adaptation: Stay adaptable to changing consumer needs and market dynamics to continually refine reverse logistics strategies.
Challenges in Reverse Logistics
The challenges in reverse logistics services are the following:
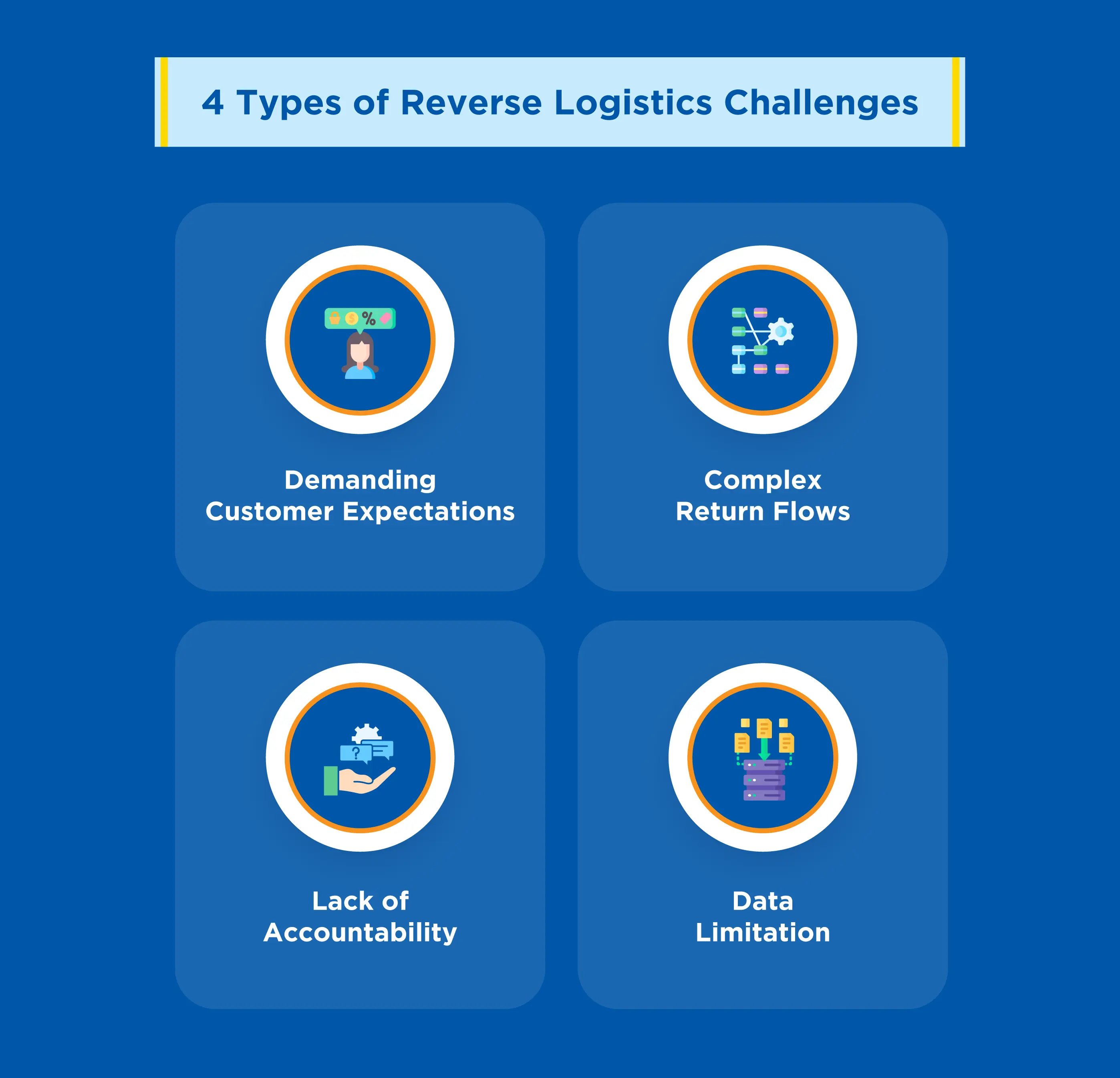
- High Costs: Managing returns, transportation, and processing can be expensive.
- Complex Coordination: Coordinating returns involves multiple stakeholders, leading to potential inefficiencies.
- Customer Satisfaction: Meeting diverse customer expectations on return policies while maintaining profitability.
- Product Quality Control: Ensuring returned products meet quality standards for resale, refurbishment, or recycling.
- Environmental Impact: Minimizing waste and carbon footprint associated with the transportation and processing of returns.
- Inventory Management: Balancing returned stock levels without affecting the supply chain negatively.
- Data Management: Collecting, analyzing, and leveraging data from returns to improve operations is challenging.
- Regulatory Compliance: Adhering to local and international regulations regarding returns, recycling, and waste disposal.
- API integration: Implementing and maintaining technology solutions, including API integration, for efficient reverse logistics processes.
- Fraud Prevention: Detecting and mitigating fraud in the return process, such as return of used or counterfeit goods.
Frequently Asked Questions (FAQs)
Why is reverse logistics important for businesses and consumers?
Reverse logistics is important for sustainability, resource optimization, customer satisfaction, and efficient returns processing, benefiting both businesses and consumers.
Can reverse logistics provide a competitive advantage to companies?
Yes, a well-managed reverse logistics system can lead to customer loyalty, reduced costs, and improved inventory management, giving companies a competitive edge.
How do companies handle the financial impact of reverse logistics?
Companies implement efficient return policies and processes to minimize losses, and invest in reverse logistics software to streamline returns and reduce costs.
What role does technology play in improving reverse logistics?
Technology, like RFID and logistics software, improves tracking, automates processes, and enhances data analysis for better decision-making in reverse logistics.
How can a company reduce the volume of returns in reverse logistics?
By improving product quality, providing accurate product descriptions, enhancing customer service, and setting clear return policies to minimize the likelihood of returns.